Understanding CNC Machines: A Comprehensive Guide to CNC Machining
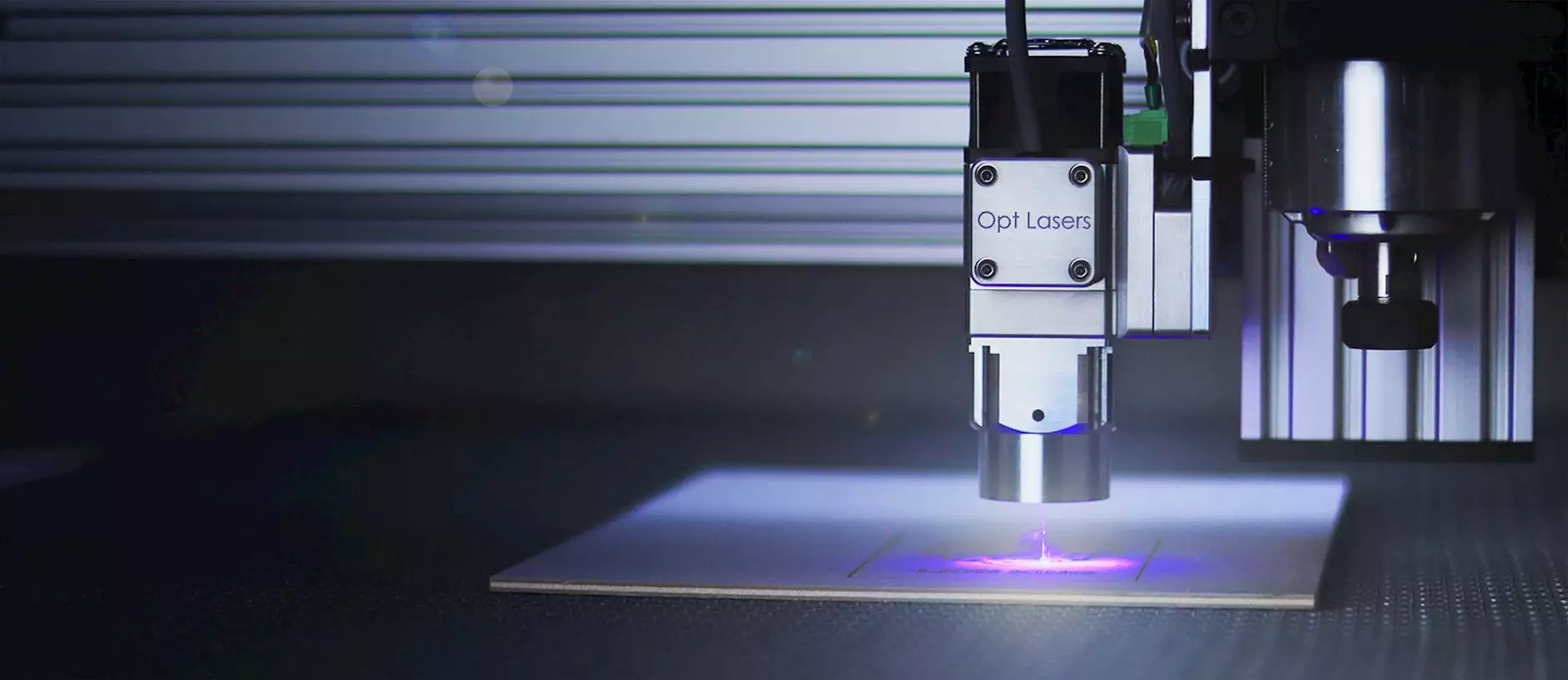
CNC machines, or Computer Numerical Control machines, are revolutionizing the manufacturing landscape through their advanced automation technology. Unlike traditional machines that relied on manual operation through handwheels or levers, CNC machines operate using sophisticated software and pre-programmed commands. This article dives deep into the world of CNC machining, discussing its history, components, software, programming, and the critical role of qualified CNC machinists.
The Evolution of CNC Technology
The journey of CNC technology can be traced back to the 1940s, when the concept of automation began to take shape. The major developments included:
- 1940s: Initial automation experiments using punched tape.
- 1950s: The emergence of numerical control (NC) machines that could be programmed.
- 1960s: Introduction of the first CNC machines, which integrated real-time computer controls.
- 1970s - Present: Continuous advancements in software and hardware have made CNC machining more precise, efficient, and user-friendly.
What Are CNC Machines?
CNC machines use a computer system to control machine tools, such as lathes, milling machines, routers, and grinders. These machines execute a wide variety of tasks, including cutting, shaping, drilling, and milling, with exceptional accuracy and repeatability.
Components of CNC Machines
Understanding the components of CNC machines is crucial for grasping how they function:
- Controller: The brain of the CNC machine, executing the commands from the programming software.
- Drive mechanisms: These translate the controller's commands into physical motion using motors and lead screws.
- Tool holder: Holds the tool in place during operation, ensuring stability and precision.
- Feedback systems: Sensors provide real-time data to the controller for adjustments to improve accuracy.
- Cooling systems: Vital for dissipating heat generated during machining to maintain optimal performance.
Understanding G-Code: The CNC Machining Language
At the core of CNC machining lies G-code, a language used to convey instructions to CNC machines. G-code commands dictate the machine’s movements, speed, tool changes, and other essential functions.
Basic Structure of G-Code
Each G-code command typically consists of several components:
- G-commands: Indicate the type of movement (e.g., G0 for rapid positioning, G1 for linear interpolation).
- Coordinates: Specify the target positions on the X, Y, and Z axes.
- Feed rates: Define how quickly the tool should move.
- Tool numbers: Identify which tool from the tool holder should be used.
Examples of G-Code Commands
Understanding some common G-code commands can provide insight into how manufacturing processes are programmed:
- G0 X10 Y10: Move quickly to the coordinates (10, 10).
- G1 Z-5 F100: Move down to Z=-5 at a feed rate of 100 units/minute.
- G28: Return to home position.
Computer-Aided Design (CAD) and Computer-Aided Manufacturing (CAM)
Two integral components that work hand-in-hand with CNC machines are CAD and CAM. These software systems streamline the design and manufacturing processes.
Computer-Aided Design (CAD)
CAD software allows engineers and designers to create detailed 2D and 3D models of parts and assemblies. These models contain precise mechanical dimensions and specifications that are crucial for the manufacturing process.
Computer-Aided Manufacturing (CAM)
Once a design is complete, CAM software translates these designs into the manufacturing instructions needed for CNC machines. The CAM system generates the G-code needed for CNC programming based on the CAD drawings.
The Importance of Skilled CNC Machinists and Programmers
The efficiency and quality of CNC machining heavily rely on skilled operators and programmers. Here’s why:
- Programming Expertise: Understanding G-code and CNC programming is critical for producing intricate parts accurately.
- Machine Operation: Skilled machinists can optimize machine settings and troubleshoot issues that arise during production.
- Quality Control: Experienced machinists monitor the machining process and ensure that parts meet specifications and standards.
Types of CNC Machines
CNC machines come in various types, each suited for specific tasks and industries:
- CNC Mills: Used for cutting and shaping materials with high precision.
- CNC Lathes: Ideal for creating symmetrical objects, such as shafts and bolts, by turning materials on a rotating axis.
- CNC Plasma Cutters: Utilize plasma torches for cutting metal with speed and precision.
- CNC Water Jet Cutters: Use high-pressure water streams to cut through a variety of materials, including metals and plastics.
- CNC Routers: Typically used for softer materials, such as wood, composites, and plastics.
Applications of CNC Machining
The versatility of cnc machining allows it to be utilized across a range of industries, including:
- Aerospace: Precision parts for aircraft components.
- Automotive: Manufacturing of engine components and body parts.
- Medical: Creating intricate parts for surgical instruments and implants.
- Manufacturing: Producing a vast array of components for various industrial applications.
- Military: Fabrication of precise components for defense systems.
The Future of CNC Machining
The future of cnc machining looks promising, with several trends expected to shape the industry:
- Increased Automation: Automation will continue to reduce human involvement, leading to higher productivity.
- Smart Manufacturing: Integration of IoT devices is expected to enhance data collection and machine monitoring.
- Advanced Materials: Development of new materials will open new possibilities for CNC applications.
- Sustainability: Efforts to make the manufacturing process more environmentally friendly will gain momentum.
Conclusion
In conclusion, understanding CNC machines is essential for anyone involved in modern manufacturing. The advanced automation technology, programming languages like G-code, and software solutions like CAD and CAM have transformed how we design and produce components. Skilled CNC machinists play a vital role in ensuring these machines operate at their best, producing high-quality parts that meet industry specifications. As technology continues to evolve, CNC machining will remain at the forefront of manufacturing innovation, driving efficiency and precision in various applications.
For more information on CNC machines and their applications, consider visiting Robocon CNC, a leader in CNC solutions.