Understanding Downhole Filters: Maximizing Efficiency in Drilling Operations
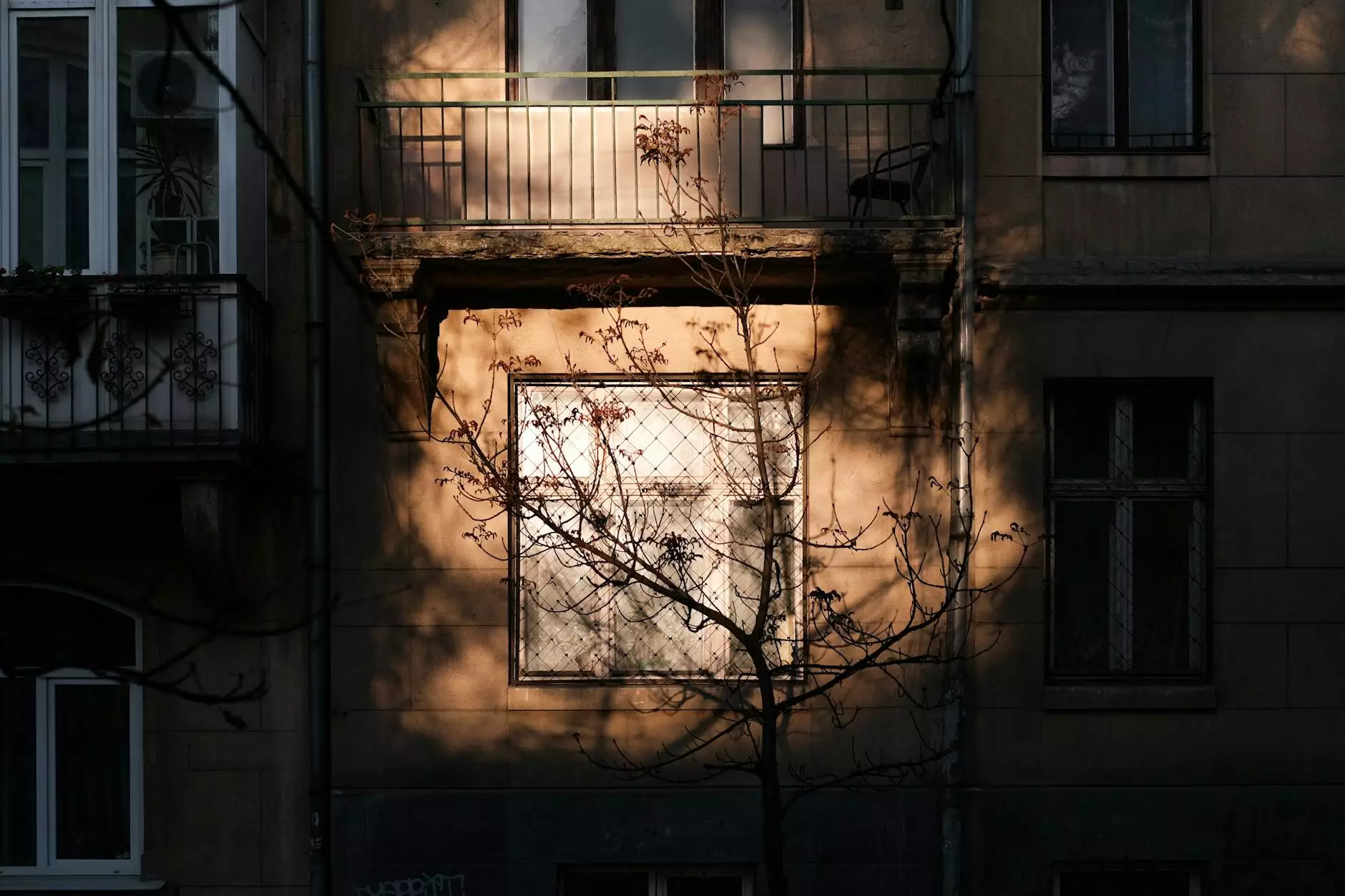
In the world of drilling and oil extraction, efficiency and performance are pivotal. Among the myriad of tools and equipment that contribute to successful drilling operations, downhole filters play a crucial role in ensuring optimal functionality. These filters are essential components in the drilling process, helping to maintain the integrity and efficiency of the operation.
What are Downhole Filters?
Downhole filters are specialized devices designed to remove contaminants and unwanted materials from the drilling fluid before it reaches the drill bit. This filtration is critical as it not only protects equipment but also enhances the overall drilling performance by ensuring that the drill bit operates in clean conditions. Typically installed in various parts of the drilling assembly, downhole filters help to maintain the viscosity and properties of the drilling mud, contributing to a smoother drilling process.
The Importance of Downhole Filters in Drilling Operations
The significance of these filters cannot be understated. Here are the primary reasons why downhole filters are vital in drilling operations:
- Protection of Equipment: Filters ensure that harmful particles do not damage sensitive drilling equipment, such as pumps and drill bits.
- Improved Efficiency: A clean drilling fluid composition leads to better performance and reduced downtime.
- Enhanced Safety: Reducing contamination minimizes the risk of hazardous incidents during drilling operations.
- Extended Tool Life: By filtering out detrimental materials, the longevity of drilling tools is significantly increased.
Types of Downhole Filters
Downhole filters come in various types, each suited to different applications and operational requirements. Understanding these types is essential for selecting the right filter for your specific operation:
1. Sand Filters
Sand filters are primarily designed to capture sand and other particulate matter in drilling fluids. They are vital in environments where the likelihood of sand ingress is high, preventing wear and tear on equipment.
2. Screen Filters
Utilizing a mesh or screen, these filters effectively separate solids from liquids. Depending on the screen mesh size, they can capture a range of particle sizes, making them flexible for different drilling conditions.
3. Magnetic Filters
Magnetic filters use magnets to attract and capture ferrous materials from the drilling fluid. This type is especially useful in operations where metal shavings may pose a risk to the equipment.
4. Cartridge Filters
These replaceable filters allow for easy maintenance and cleaning. Cartridge filters can be tailored to different filtration needs based on the size and nature of the contaminants.
Applications of Downhole Filters
Downhole filters find applications in various areas of the drilling process. Here are some key applications:
- Oil and Gas Extraction: In the oil and gas sector, maintaining clean drilling fluids is crucial for preventing equipment failure and ensuring efficient resource extraction.
- Geothermal Drilling: In geothermal operations, filters help manage the high levels of mineral deposits typically present in drilling fluids.
- Water Well Drilling: Downhole filters ensure the water extracted is clean and free of contaminants, particularly important in drinking water operations.
Choosing the Right Downhole Filter
Choosing the appropriate downhole filter for your drilling operation requires careful consideration of several factors:
- Type of Contaminants: Understanding the types of contaminants in your drilling fluid will guide the selection process.
- Flow Rate: Assess the flow rate of the drilling fluid to ensure the filter can handle the volume without clogging.
- Temperature and Pressure: The operational environment’s temperature and pressure can affect the choice of material and design you should consider for the filter.
Benefits of Using Downhole Filters
The implementation of downhole filters in any drilling operation offers numerous benefits:
- Cost-Effective: By preventing equipment damage, downhole filters can save significant repair costs and downtime.
- Enhanced Performance: Clean drilling fluids improve the overall performance of the drilling rig, enhancing the rate of penetration.
- Improved Environmental Compliance: Effective filtration reduces the risk of contaminating surrounding environments, aiding in regulatory compliance.
Common Challenges and Solutions
Despite their benefits, the use of downhole filters can present certain challenges. Understanding these challenges, along with potential solutions, is essential for ensuring successful implementation in drilling operations.
Challenge 1: Clogging
Clogging of filters is a common issue, especially in high-solid environments. Regular maintenance and timely replacement of filters can mitigate this issue. Additionally, selecting the right mesh size based on the expected particle size can greatly reduce the risk of clogging.
Challenge 2: Difficult Access for Maintenance
Accessing downhole filters for cleaning or replacement can be challenging, particularly in deep drilling applications. Employing filters with easy maintenance mechanisms, such as cartridge filters, can alleviate this concern and ensure the operations remain smooth.
Challenge 3: Selecting the Right Filter for Varied Conditions
Every drilling operation is unique, necessitating a tailored approach to downhole filtration. Conducting thorough analysis and tests on the drilling fluid and anticipated contaminants will lead to better filter selection that meets specific operational needs.
The Future of Downhole Filters
As technology progresses, so too do the designs and capabilities of downhole filters. The future of these essential components in drilling operations is promising, with advancements predicted to enhance efficiency, durability, and ease of use.
1. Advanced Material Use
The development of new materials that withstand extreme conditions while providing better filtration efficiency is set to revolutionize downhole filters.
2. Smart Technologies
Integration of smart technologies, such as IoT sensors, will allow real-time monitoring of filter performance, enabling proactive maintenance and management of drilling fluids.
3. Eco-Friendly Solutions
As environmental concerns grow, the demand for filters that not only improve operational efficiency but also minimize environmental impact will drive innovation in downhole filter technologies.
Conclusion
In summary, downhole filters are indispensable to modern drilling operations, providing essential benefits that enhance the efficiency, safety, and cost-effectiveness of drilling projects. By choosing the right filter, understanding their applications, and embracing emerging technologies, drilling companies can significantly improve their operational performance. As the industry continues to evolve, staying informed about the latest advancements in filtration technology is essential for maintaining a competitive edge.
For those in the drilling business, investing in high-quality downhole filters is not merely a safeguard but a strategic move towards achieving success in a highly competitive market. To learn more about downhole filters and other high-quality products that can boost your drilling operations, visit Maverick Drilling.