CNC Lathed Parts: Revolutionizing Metal Fabrication
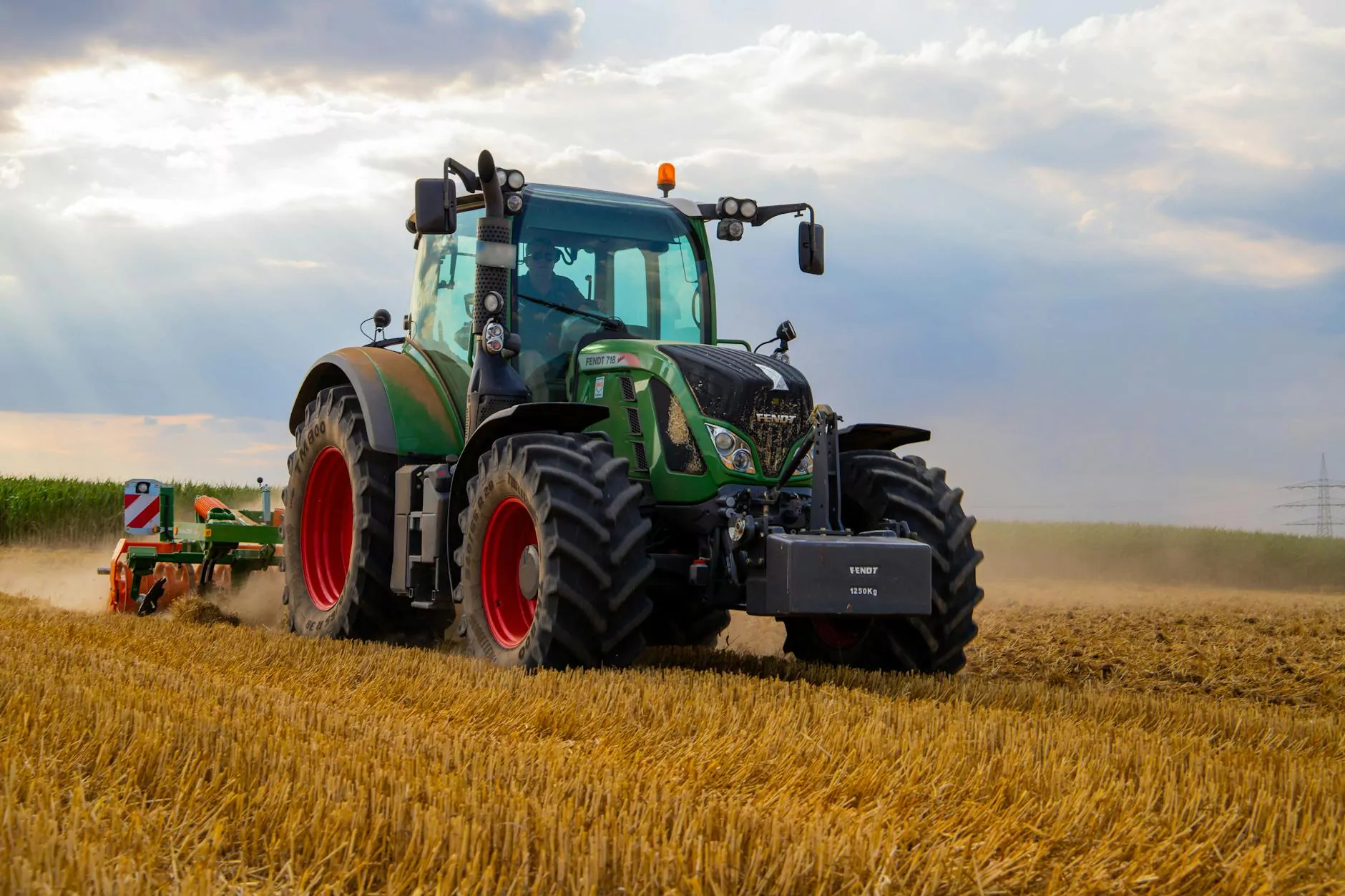
The world of manufacturing is constantly evolving, and at the forefront of this evolution are CNC lathed parts. These precision-engineered components play a pivotal role across various industries, ensuring that products are made to the highest standards of accuracy and quality. In this comprehensive guide, we will explore the intricacies of CNC lathed parts, their manufacturing processes, applications, and the advantages they bring to businesses, particularly in the realm of metal fabrication.
1. What are CNC Lathed Parts?
CNC, or Computer Numerical Control, is a method used to automate machine tools through computers executing pre-programmed sequences of machine control commands. CNC lathed parts are components that are created using a CNC lathe, a sophisticated machine tool that shapes materials—usually metal or plastic—by removing material from a rotating workpiece.
This process allows for high precision and repeatability, making it ideal for manufacturing parts that require tight tolerances and complex geometries.
1.1. The CNC Lathe Explained
A CNC lathe operates by rotating the workpiece while a cutting tool is moved against it. The principle of operation includes:
- Turning: Material is removed by a cutting tool to create cylindrical shapes.
- Facing: The cutting tool is applied perpendicular to the material to create flat surfaces.
- Drilling: Holes are created by using a specialized drill bit.
The versatility of CNC lathes makes them a cornerstone in precision machining, facilitating the production of a variety of CNC lathed parts from a range of materials.
2. The Manufacturing Process of CNC Lathed Parts
The process of manufacturing CNC lathed parts involves several key stages:
2.1. Design and Programming
The first step in crafting any CNC lathed parts is designing the component using Computer-Aided Design (CAD) software. This software allows engineers and designers to create intricate 3D models that are then translated into machine code using Computer-Aided Manufacturing (CAM) software. This code instructs the CNC machine on how to shape the material accurately.
2.2. Material Selection
Choosing the right material is crucial. Common materials used include:
- Aluminum
- Steel
- Copper
- Plastics
The properties of the material selected will determine the feasibility of the design and the application of the final part.
2.3. Machining Process
During the machining phase, the CNC lathe executes the programmed instructions, transforming the raw material into the finished part. This phase is characterized by:
- Precision: Ability to achieve tight tolerances as low as a few micrometers.
- Consistency: Each part produced matches the specifications set in the design phase.
- Efficiency: High-speed operations reduce turnaround times significantly.
2.4. Quality Control
After the machining is completed, parts undergo rigorous quality control checks to ensure they meet both dimensional and aesthetic standards. This includes:
- Dimensional inspections using precision instruments.
- Visual inspections to detect any surface flaws or defects.
- Functional tests to ensure parts operate as intended.
3. Applications of CNC Lathed Parts
CNC lathed parts are integral to multiple industries due to their versatility and precision. Here are some prominent applications:
- Aerospace: Manufacturing parts that require lightweight and durable components designed for performance under extreme conditions.
- Automotive: Production of high-precision components like gears, pulleys, and shafts.
- Medical: Creating precise instruments and components that meet stringent health and safety standards.
- Electronics: Fabricating intricate parts for devices, including casings and connectors.
4. Advantages of Using CNC Lathed Parts
There are several key benefits to utilizing CNC lathed parts in manufacturing:
4.1. Precision and Accuracy
CNC technology allows for incredibly precise cuts and shapes, ensuring that every part produced adheres to strict specifications.
4.2. Reduced Manufacturing Time
The automation involved significantly speeds up the production process, reducing lead times and increasing output.
4.3. Cost-Effectiveness
Although the initial investment in CNC technology can be substantial, the long-term savings in labor and material waste make CNC machining a cost-effective choice in the long run.
4.4. Flexibility and Scalability
CNC lathes can easily adapt to producing different designs, making them suitable for both small runs and large-scale production without the need for extensive retooling.
5. Choosing the Right Partner for CNC Lathed Parts
When selecting a company for your CNC lathed parts, it's essential to consider several factors to ensure that you receive the best quality components:
5.1. Experience and Expertise
Look for manufacturers with a proven track record in CNC machining, specifically in producing parts similar to what you require.
5.2. Technology and Equipment
Ensure the company has modern CNC machinery capable of producing high-precision parts efficiently.
5.3. Quality Assurance Practices
Investigate their quality control measures and certifications to understand their commitment to excellence.
5.4. Customer Support
A reliable partner should offer excellent customer service, assisting with everything from design to delivery and beyond.
6. Conclusion: The Future of CNC Lathed Parts
As industries continue to evolve, the demand for CNC lathed parts is expected to grow. Companies like deepmould.net are at the forefront of this evolution, employing advanced technologies and highly skilled professionals to produce top-quality components. Understanding the features, benefits, and applications of CNC lathed parts is crucial for any business looking to improve its manufacturing processes.
By choosing CNC lathed parts, your business can harness the power of modern manufacturing, ensuring efficiency, precision, and productivity in every project.