Understanding the Imperative Role of CNC Precision Machining Factories in Modern Manufacturing
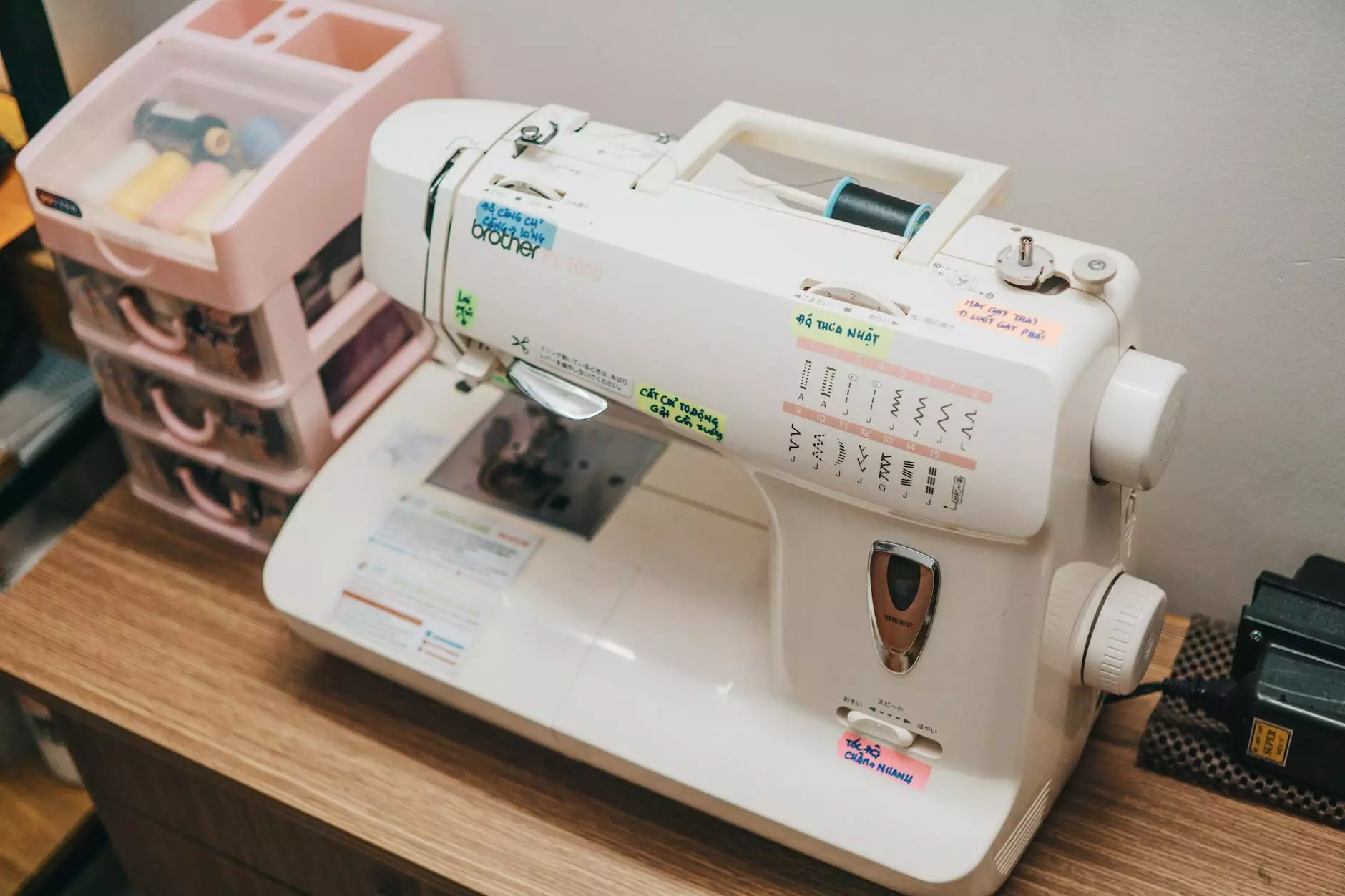
CNC precision machining factories play a crucial role in today’s manufacturing landscape. Their contribution to various industries cannot be understated, as they offer unparalleled accuracy, efficiency, and flexibility. With the increasing demand for high-quality metal fabrication, these factories have become essential for meeting the sophisticated needs of modern production. In this article, we will delve into the numerous benefits of CNC precision machining, explore its processes, and understand its impact on the manufacturing sector.
The Essence of CNC Precision Machining
CNC, or Computer Numerical Control, is an advanced technology that automates the control of machine tools through a computer program. This innovation has transformed traditional machining by providing several key benefits:
- Enhanced Accuracy: CNC machines operate based on precise programming, resulting in consistent and highly accurate parts.
- Automation: With automated processes, CNC machining minimizes human error and reduces production time significantly.
- Complex Geometries: CNC precision machining can easily work with complex designs that are often difficult to achieve with conventional methods.
- Versatility: Suitable for a variety of materials including metals, plastics, and composites, making it ideal for diverse applications.
Benefits of CNC Precision Machining Factories
The advantages of utilizing CNC precision machining factories are manifold. Below, we outline some of the most significant benefits:
1. Increased Production Efficiency
The automation provided by CNC machinery allows for rapid production cycles. Unlike manual machining, CNC machines can operate continuously, leading to greater output. The ability to run multiple machines concurrently ensures that manufacturers can meet high volume demands without sacrificing quality.
2. Cost Reduction
Investing in a cnc precision machining factory leads to long-term cost savings. The initial investment in CNC technology can be substantial, but the reduction in labor costs, waste, and rework ultimately outweighs this expenditure. Furthermore, as production becomes more efficient, manufacturers can benefit from economies of scale.
3. Superior Precision and Quality
One of the standout features of CNC precision machining is its ability to produce parts with extreme precision. This level of accuracy is vital in industries such as aerospace, automotive, and medical devices, where tolerances can be tight. CNC machines can achieve tolerances of ±0.001 inches or better, thus ensuring high-quality outputs consistently.
4. Flexibility and Customization
CNC precision machining allows for easy modifications in design without significant downtime. Manufacturers can implement changes quickly, enabling them to respond to market needs and customize products according to client specifications. This adaptability is crucial in today’s fast-paced business environment.
5. Improved Safety
Automating processes through CNC machines reduces direct human involvement in manufacturing operations, significantly lowering the risk of accidents. Factory environments are safer as workers spend less time operating heavy machinery directly. Enhanced safety measures prevent injuries and lead to a more productive workplace.
The CNC Machining Process: A Closer Look
To truly appreciate the role of a cnc precision machining factory, it’s essential to understand the steps involved in the machining process:
1. Designing a CAD Model
The journey begins with a Computer-Aided Design (CAD) model that outlines the specifications of the desired part. This detailed plan serves as the blueprint for the entire process.
2. Setting Up the CNC Machine
Once the CAD design is complete, the CNC machine is set up. This includes loading the appropriate tools and material, as well as configuring the machine settings according to the specifications derived from the CAD model.
3. Programming the CNC Machine
Next, a Computer Numerical Control program is generated from the CAD file. This program translates the design into a language that the CNC machine can interpret, guiding it through each step with precision.
4. Machining Operations
With everything in place, the actual machining begins. The CNC machine performs various operations like milling, turning, and drilling, consistently following the programmed instructions to produce the desired part.
5. Quality Control
After machining, comprehensive quality control measures are implemented to ensure that each part meets the required specifications and tolerances. This step is paramount for maintaining the quality assurance that clients expect.
Industry Applications of CNC Precision Machining
The versatility of CNC precision machining means it has applications in a wide array of industries, including:
- Aerospace: Producing high-precision components that demand rigorous standards for safety and performance.
- Automotive: Manufacturing intricate parts that fit precisely and operate reliably under demanding conditions.
- Medical Devices: Creating custom parts and equipment with high levels of precision crucial for patient safety.
- Industrial Machinery: Developing complex parts that play vital roles in industrial operations and heavy machinery.
Choosing the Right CNC Precision Machining Factory
When selecting a cnc precision machining factory, several factors should be considered:
1. Expertise and Experience
Assess the factory’s experience in the industry. A company with a robust portfolio demonstrates reliability and capability.
2. Technology and Equipment
The latest machining technology enhances precision and efficiency. Ensure the factory invests in state-of-the-art CNC machines and tools.
3. Quality Assurance Processes
Inquire about their quality control processes. An effective quality assurance system is crucial for delivering high-quality products consistently.
4. Customer Service
Good customer service is indicative of a reputable company. Ensure they are responsive and willing to address your concerns.
Conclusion
In conclusion, a cnc precision machining factory stands as a pillar of modern manufacturing, offering numerous advantages such as enhanced efficiency, quality, and flexibility. As demand for high-quality precision components continues to grow across various industries, the significance of these factories is more pertinent than ever. By effectively leveraging CNC technology, manufacturers can optimize production, reduce costs, and ultimately enhance service delivery. Investing in CNC precision machining is not merely a choice; it is a necessity for businesses aspiring to thrive in the competitive market.
For more information about CNC precision machining and to explore how it can benefit your business, visit deepmould.net.